Managing PAT Testing in the Workplace
This article is aimed at those responsible for ensuring the safety of electrical equipment in the workplace.
Legal Responsibilities
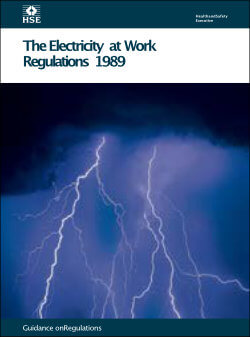
The Electricity at Work Regulations 1989 apply to all work activities involving electrical equipment. These regulations impose a legal duty on employers, self-employed, and employees to manage risks arising from the use of electricity. Risk control measures should be proportionate and based on a risk assessment. This involves identifying hazards and implementing sensible measures to manage these risks in the workplace. Read our article about the Legal Requirements of PAT Testing for more details.
What is Portable Appliance Testing (PAT)?
Portable Appliance Testing (PAT) is a recognised procedure for checking electrical equipment to identify possible hazards. It involves visual inspections and electrical tests to verify the safety of electrical equipment. The Institute of Engineering and Technology provides guidelines for these inspections and tests in their publication, "In-Service Inspection and Testing of Electrical Equipment."
What Equipment Needs to be Tested?
Despite the term "Portable Appliance Testing (PAT)", the inspection and testing isn't confined to portable equipment. It encompasses all equipment operating between 50 Vac and 1,000 Vac that is connected or could be connected to the electrical supply. While most appliances connect to the supply via a plug and socket, some equipment may be permanently connected to the supply via a fused spur.
How often should it be Done?
Contrary to popular belief, there aren't predetermined intervals for PAT testing. Instead, it should be based on a risk assessment approach. Factors to consider in this assessment include the type of equipment, how it's used, the working environment, and frequency of use, among others. High-risk equipment, like workshop hand tools, will require more frequent checks than low-risk equipment like office IT equipment. For more insights, visit our guide on Risk Assessment for PAT Testing Frequency.
Maintaining Test Records
While it isn't a legal requirement to maintain a record of inspection and testing, doing so can be a valuable management tool. These records can provide insights into areas of use or types of equipment subjected to above-average wear or damage. This information can be used to determine if more frequent testing is needed or if the equipment selection is appropriate. Test records should generally include a description of the equipment, identification details such as a serial number or asset number, the location, and the results of the inspection and tests.
Labelling
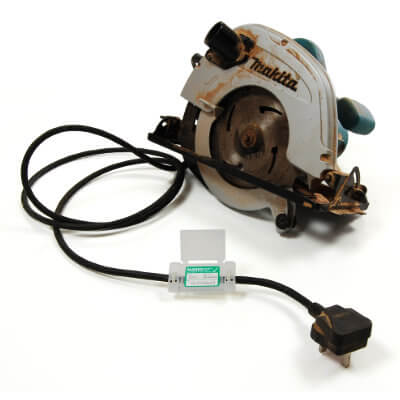
Labelling inspected and tested equipment serves as an easy reference that the equipment is safe. Labels can also provide a useful means of cross-referencing the item to the test records by including an asset number. It's important to ensure that the label is sufficiently robust to survive the period between retests. Equipment used in an arduous environment, such as power tools on a construction site, may require additional protection such as using a Snaptag label holder.
User Checks and Staff Training
Often overlooked, user checks, which involve simple visual inspections by employees, play a vital role in identifying potential hazards. Training staff to look for apparent defects or damage before using an electrical device can further reduce the risk of electrical accidents. Training should provide guidance on performing effective user checks, identifying potential electrical hazards, and understanding the steps to report or rectify issues. Learn how to carry out a User Check for PAT Testing.
New Equipment
While new equipment doesn't typically require testing, a visual inspection before use is advisable to verify that it hasn't been damaged during transit. Once checked, the new equipment should be added to your equipment register, and a risk assessment should be conducted to determine the appropriate frequency for future inspections and testing.
In addition, a purchasing policy for new electrical appliances is recommended. Ensure that equipment is sourced from reputable suppliers to avoid the risks associated with counterfeit and substandard electrical items. Currently, the UK faces a significant challenge with counterfeit and potentially dangerous electrical items being sold online through platforms like eBay, Amazon, and Alibaba. By establishing procurement processes, you can help safeguard your workplace against these electrical safety hazards.
Personal Electrical Equipment Policy
Staff members often bring personal electrical devices, such as mobile phone chargers and portable heaters into the workplace. You should consider implementing a policy to manage this, ensuring that personal items are also safe for use and do not pose any electrical risks. As this equipment is usually of unknown origin, age and condition, it's recommended that it is inspected and tested before being used in the workplace.
Outsourcing PAT Testing
For many businesses, outsourcing PAT testing to a third-party service is a convenient solution. However, it's essential to agree on test intervals, labelling, and record-keeping practices beforehand to ensure they meet your requirements. Clear procedures for handling failed equipment and repairs should also be in place.
In-House PAT Testing
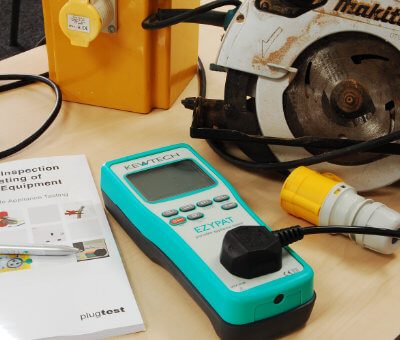
Performing inspection and testing internally can offer greater flexibility and additional benefits, such as minimising disruption, improving quality control, ensuring equipment availability, and potentially saving costs over time. The person performing the testing must be competent, meaning they must be appropriately trained and possess the necessary knowledge and skills to perform the tests and interpret the results correctly. If you decide to conduct PAT testing in-house, consider our PAT Competent Person course, which equips students with the practical skills and technical knowledge required for in-house PAT testing.
Conclusion
Whether you choose to outsource your PAT testing or handle it in-house, as a duty holder you have the overall responsibility for overseeing the safety of the electrical equipment within the workplace. It involves not only conducting the necessary tests but also establishing a system of maintenance, but it does not need to be overly complicated, it is all about taking sensible and proportionate measures to control the risks in the workplace.
Further reading
- The IET Code of Practice For In-Service Inspection and Testing of Electrical Equipment provides information on both the management of PAT testing and also the practical details of how to perform the inspection and tests.
- HSE - Maintaining Portable Electrical Equipment outlines a recommended maintenance plan for a system of user checks, and visual inspection and testing.
- HSE - Maintaining Portable Electrical Equipment in Low-Risk Environments. This document provides simple and practical advice on managing electrical equipment in low-risk environments such as offices and shops.